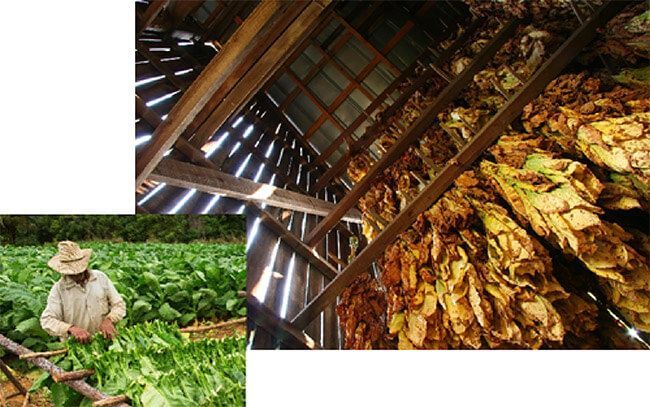
The process of growing Cuban tobacco is complex and slow: a minimum of 12 months, a full year, must pass before the leaf is ready to make a cigar. This is known as the veguero year.
Each stage requires its time and the expert dedication of the farmers. Taking care of every detail, without rushing.
The following is the path that each one of those leaves goes through, from the preparation of the soil to the final packaging.

To achieve the highest quality in Cuban tobacco, it is necessary to begin by ensuring the nutritional elements of the land, conserving soil moisture and planting on flat land. The soil and climate of Cuba are the factors that distinguish Cuban tobacco as the best in the world. The preparation of the land is carried out in the rainy season, between the months of June and September.

The period between sowing the seed and the end of the harvest is about 17 weeks for covered tobacco (wrapper) and 16 for tobacco in full sun (binder and filler). It begins in September with the planting in the nursery, follow by, a week later germination and, after twelve days, pest control.
At the end of October, the seedlings are ready to be planted out from the seedbed to the tobacco plantation. For 40 days the plant matures and when it reaches the desired height, the top bud is removed to concentrate the force on the development of larger leaves. It is what is known as the “desbotonado”. At that time, harvesting can begin, a demanding task, as each leaf must be harvested by hand.
In total, four months during which the leaves that will serve to make the best tobacco in the world are painstakingly developed.
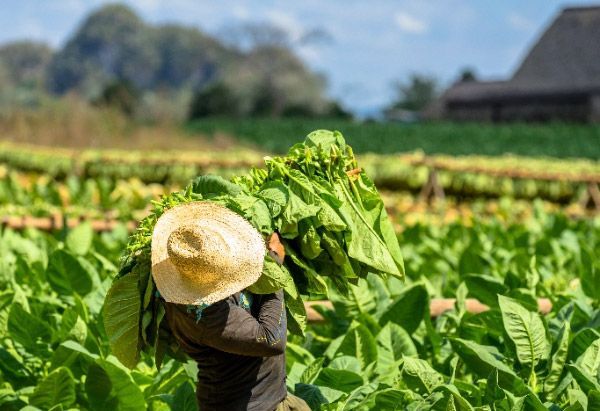
Around 40 days after planting out, harvesting can begin. Keep in mind that this is a task that is done by hand, when you can only take two or three leaves at a time and only from the same part of the plant and remembering that a few days must elapse between the collection of each part. If we do the math, the result is that to harvest a single tobacco plant in its entirety, it takes about 30 days.
After the harvest, the classification of the leaves is considered in order to respect the binding of each brand. Afterwards, the leaves are taken to the tobacco houses to begin their natural drying.
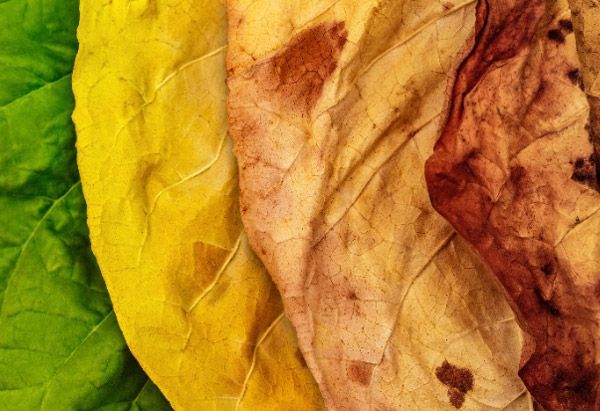
The freshly harvested leaves are taken to traditional Curing Barns (Casas de Tabaco), where they are air-dried for about 50 days to remove their moisture. During those two months or so the tobacco is completely dependent on the effects of the weather, and it is necessary to constantly adjust ventilation and lighting to compensate for natural variations in temperature and humidity.
And when we talk about how to dry tobacco leaves, we must mention one of the most characteristic processes: threading. In this step, the leaves are joined by a thread, in pairs, and are hung next to each other on racks (“cujes”) in the barn. The resulting image is very recognizable, with that mixture of shades of the leaves. Throughout this slow curing period, the initial green of the tobacco plant is transformed, due to oxidation, into a coppery brown color.
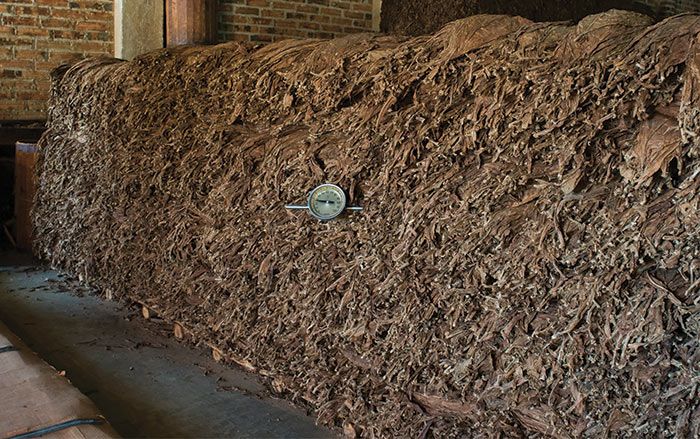
Once cured, the leaves are tied in bundles known as sheaves and taken to the collection and processing houses for fermentation. Fermentation is a 100% natural process that serves to expel ammonia and chlorine from tobacco leaves and transform their sugars. This is essential to obtain leaves of the quality required for Cuban cigars. During fermentation, the leaf expels impurities, reduces acidity, tar, and nicotine, softens the flavor of the filler, and evens out the color of the wrapper. The leaves that grew in the highest part of the plant need a longer fermentation period because they are thicker and richer in oils. The length of time the leaf is allowed to ferment will determine its flavor complexity and strength.
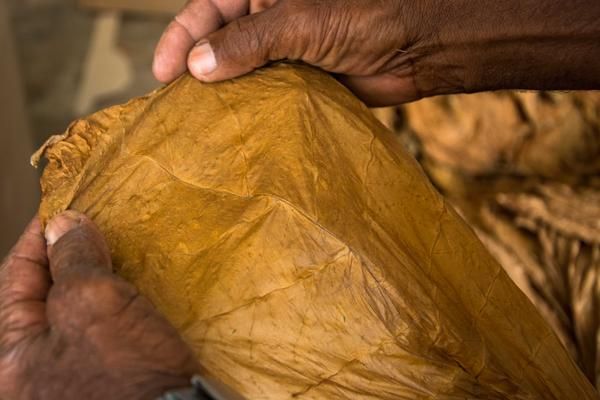
After fermentation, the leaves are chosen based on the use that will be given to them in the manufacturing process according to three criteria: size, color, degree of quality and texture. Wrapped leaves receive careful attention. The leaves for filler and binder are chosen and grouped into three sizes and three essential categories of flavor or times that are later combined in the blend: light, dry and binder.
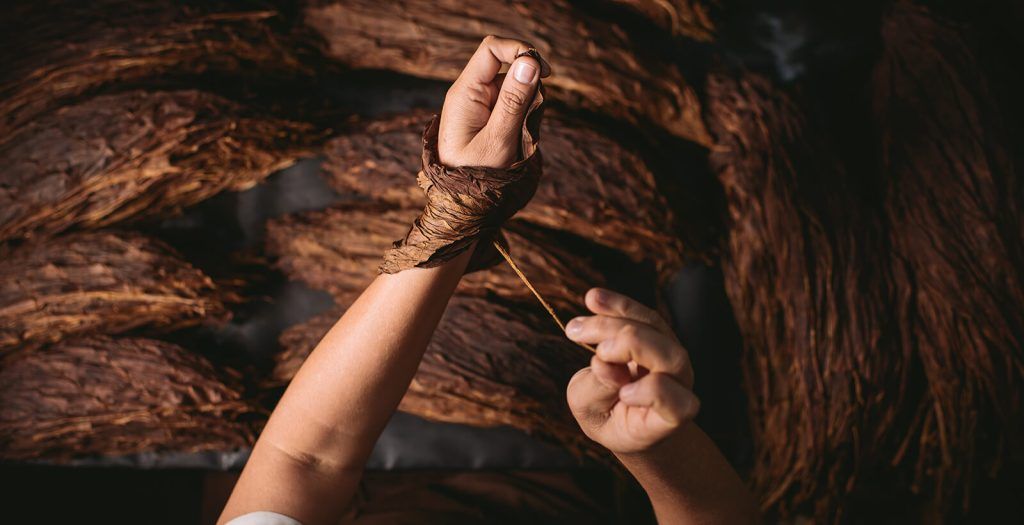
The filler and binder, once classified, are de-stemmed (the wrapper itself subsequently de-stemmed in the factory). First, they are moistened to facilitate the task. Secondly, the destemmer tears the portion of the central vein that corresponds to each type of leaf, regroups it by size and characteristics and finally iron between the boards.
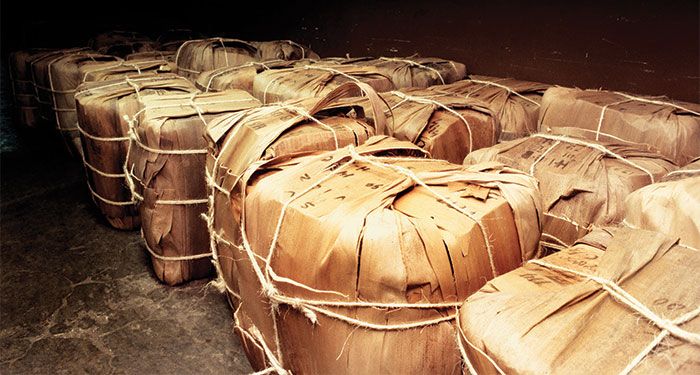
Now it is time to pack the leaves and move them to the warehouse, where they will undergo the patient final ageing process. The filler and binder leaves are packed in containers called pacas, while the wrapper leaves are packed in so-called thirds, made with yagua (the bark of the Royal Palm). The ageing process allows them to reach an ideal balance in aromas and flavors.
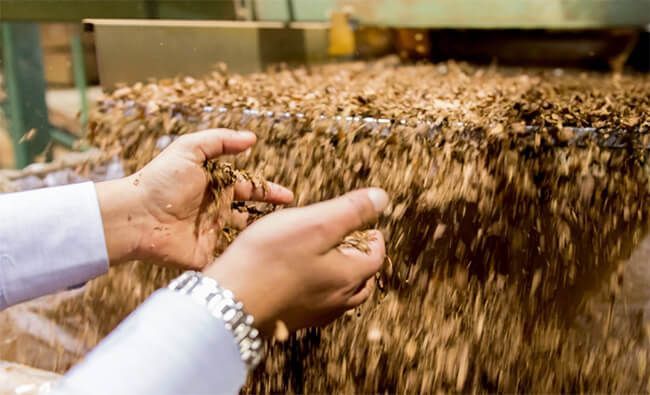