The first news about the introduction of the mechanization of tobacco production in Cuba dates from the middle of the 20th century and in particular from the end of the Second World War.
However, its consolidation began in 2001, the year in which the productive activities of Internacional Cubana de Tabacos, S.A., the company responsible for carrying out the production of mechanized tobacco in Cuba, began.
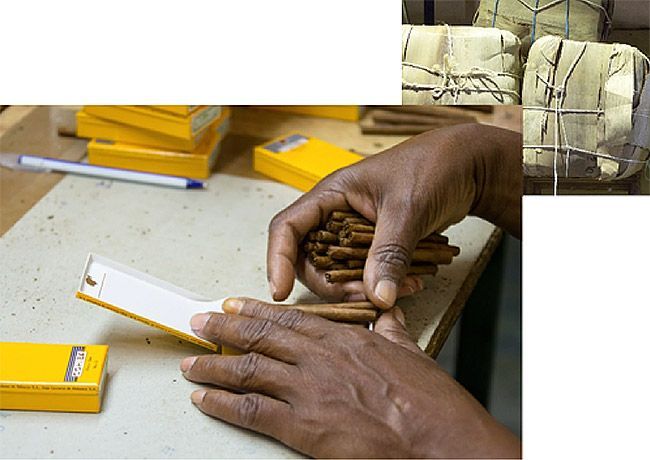
Manufacturing process
If you have ever wondered how Cuban mini cigars are made, here you can discover the different stages of their manufacturing process.
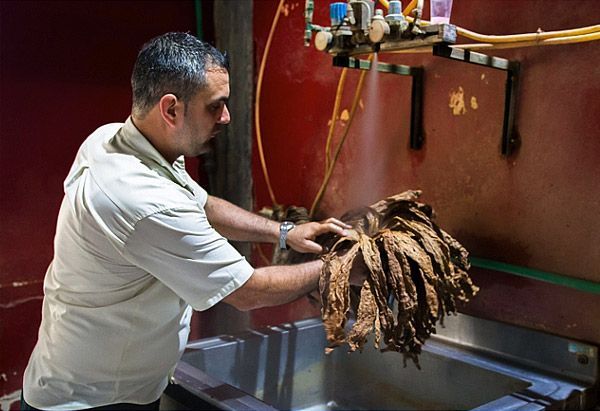
The production process begins with the preparation of the filler. The preparation of the filler is a phase of great importance since it will determine the aroma, flavor, and final strength of the cigar. Each brand has a unique blend, which is why a rigorous control of the proportions in the mixture of the different varieties of tobacco most be guaranteed so as not to alter their characteristics.
After weighing the component leaves of each blending, they are passed through a mixing cylinder that has moisture sprinklers. After mixing, they will be left to rest for 24 hours. After this time, the mixture goes to the mixers where the leaves are fragmented, the veins are separated and the dust generated is extracted, thus obtaining the casing, which is left to rest for a period of 72 hours to homogenize its humidity.
The binder leaf wraps the filler and with it forms the bundle, while the wrapper leaf will give the final finish to the cigar, giving it a perfect texture. Both sheets are manipulated in the wetting and preparation area: after wetting the sheets of the wrapper and letting them rest, they are ironed and classified. The binder follows a similar process, although without classification.
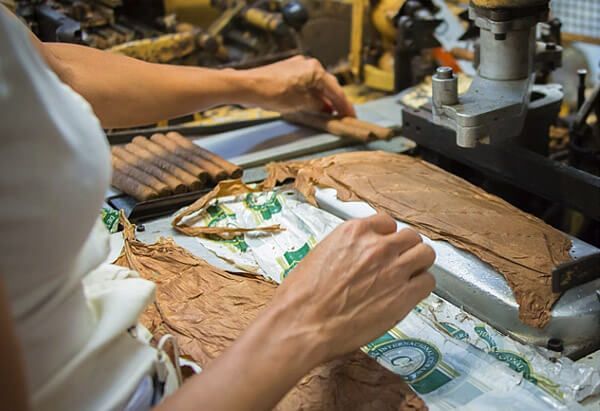
Once the raw materials are ready, the cigars are made in a machine rolling workshop, giving them different formats. The twisting process is carried out using two bundling systems:
Traditional system uses a machine with a hopper to feed the chippings and two parts connected to each other, one in charge of placing the binder and forming the bundle and the other where the wrapper is placed.
Bobbin machine is a system very similar to the traditional one with the only difference being that the task of the operators is replaced by coils of binder and wrapper cuts.
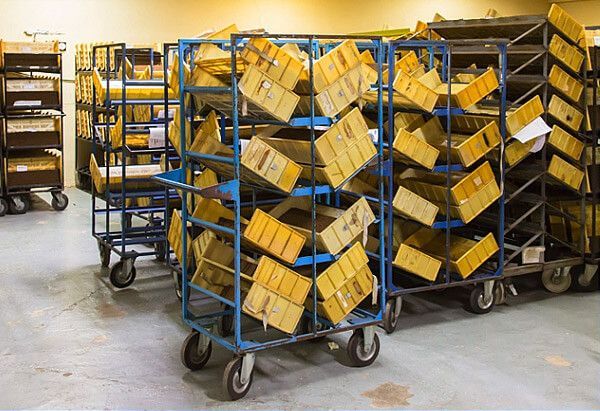
The already rolled cigar rests in a drying chamber until it reaches the desired degree of humidity. In addition to humidity, it is important to control the granulometry, that is, the size distribution of the elements that make up the cigar, which directly affects the suction of the tobacco. These controls are carried out by the Quality Management Department, which is equipped with the technology required to ensure compliance with the quality parameters of our cigar.
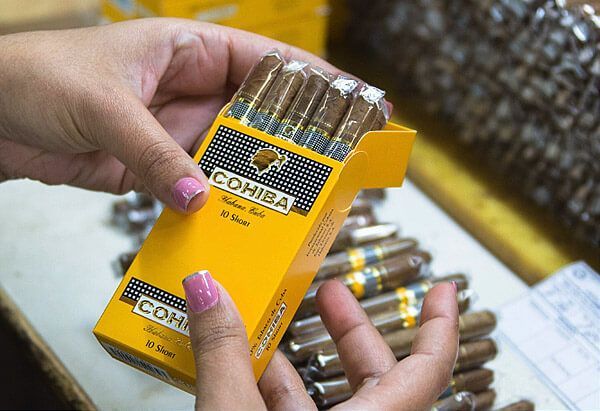
To meet the quality standards required of Cuban mini cigars, it is important to take care of every detail of their presentation. Currently, this process is carried out both manually and mechanized, although a greater number of machines are gradually being introduced in order to carry out the entire packaging process mechanically.
The ultimate objective of this phase is that the final product meets all the aesthetic and quality parameters, guaranteeing that it reaches the consumer in optimal conditions.
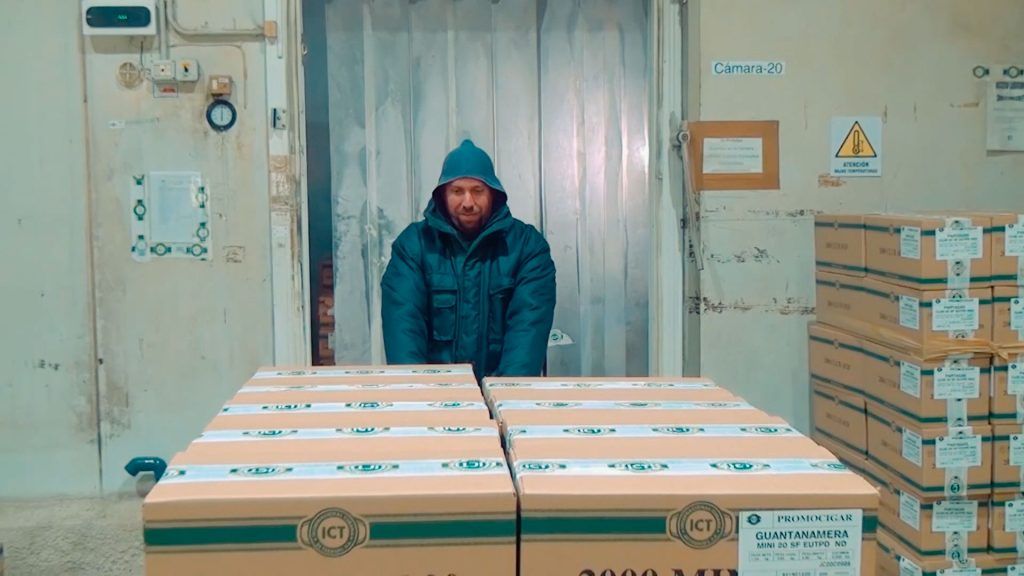
It’s time for disinfection. The process used does not use any chemical product, so it is completely harmless, 100% natural and respectful of the environment. Cigars, already packaged for sale, are frozen at -20°C for 120 hours (five days) before moving to the finished product warehouse. This process allows the elimination of any insect and parasite in any of its stages.
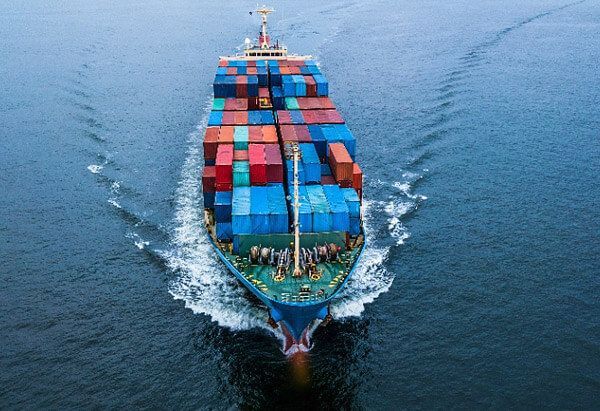
The process ends with the export and sales to the markets. Most exports are made by sea in refrigerated containers at -20 °C, although many are also shipped by air.
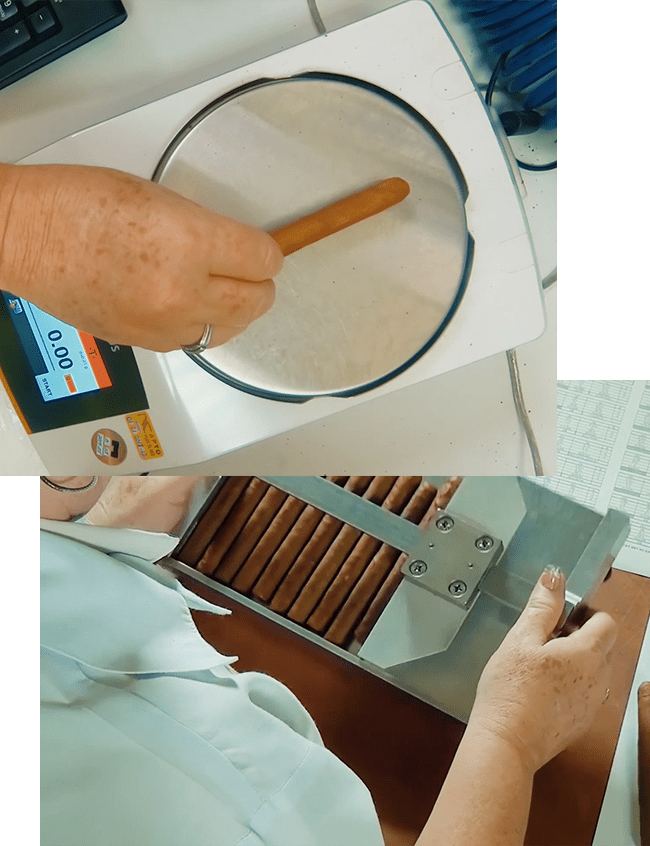
Strict quality control
All phases of the production process of mechanized Cuban cigars are supervised by a quality management specialist, who is in charge of guaranteeing compliance with the specifications defined for the production process. For this, he has the support of a laboratory equipped with the latest technology that allows each quality parameter to be checked with precision.
In order to improve both the processes and the quality of the cigars, a strict quality control system based on the ISO NC 9001:2001 standard has also been implemented, which guaranteeing the highest quality standards to customers.
All these is a very complete process where the maximum care of all the details makes each Cuban mini unique.